The Problem
Traditional gym equipment, whether free weights, cable machines, or other mechanical resistance mechanisms, operates on fixed resistance. But as we workout, our performance isn’t static—muscles fatigue, movement speed fluctuates, and force application varies through a lift.
To create a truly adaptive workout system, we needed a means of measuring force dynamically that could provide instant feedback to the machine’s control system.
We identified load cell technology as the ideal approach. The challenge was finding a precise, durable, and manufacturable force sensor that could integrate seamlessly into our Adaptive Functional Trainer (AFT) concept.
Evaluating Load Cell Geometries
To determine the best design, we explored three distinct load cell geometries, each with its own strengths and weaknesses.
1. S-type Load Cell
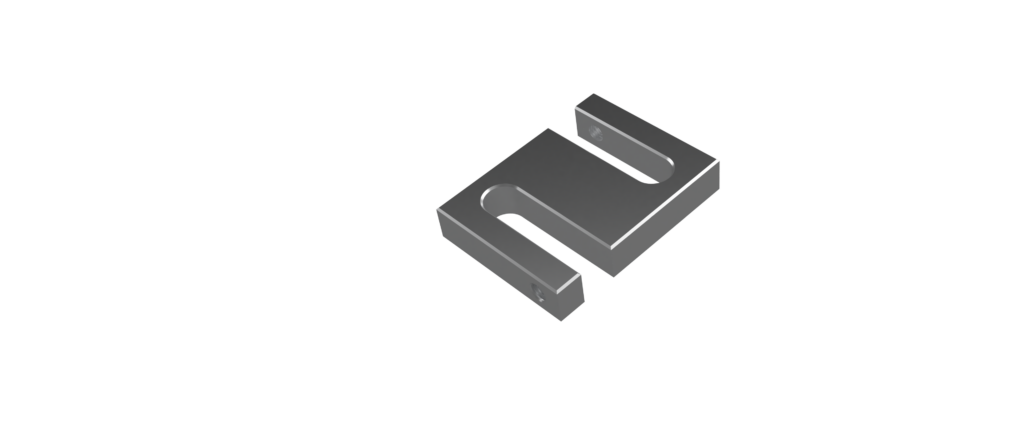
S-type load cells are among the most widely used force sensors due to their ease of manufacturing and ready availability. Their compact shape allows them to be easily integrated into a variety of mechanical setups, making them a tempting choice. However, these sensors are typically optimized for either compression *or tension—not both simultaneously. In our application, where the load cell experiences dynamic bidirectional forces, S-type sensors introduced inconsistencies in force readings, making them unsuitable for real-time feedback in an adaptive system.
2. Wishbone Load Cell
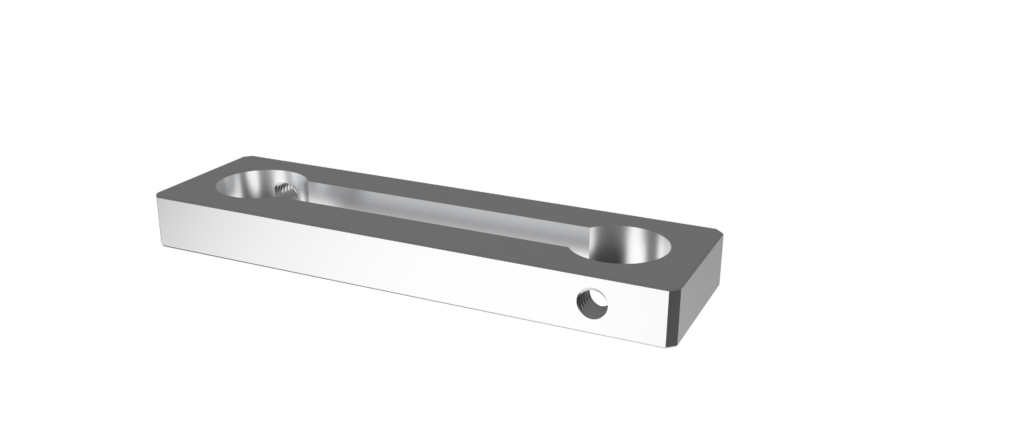
Wishbone-style load cells, while mechanically simple, require a larger displacement to generate a significant measurable change in resistance. Flexing within the wishbone structure caused variations in strain measurements, making real-time feedback unreliable.
3. Tube-Type Load Cell
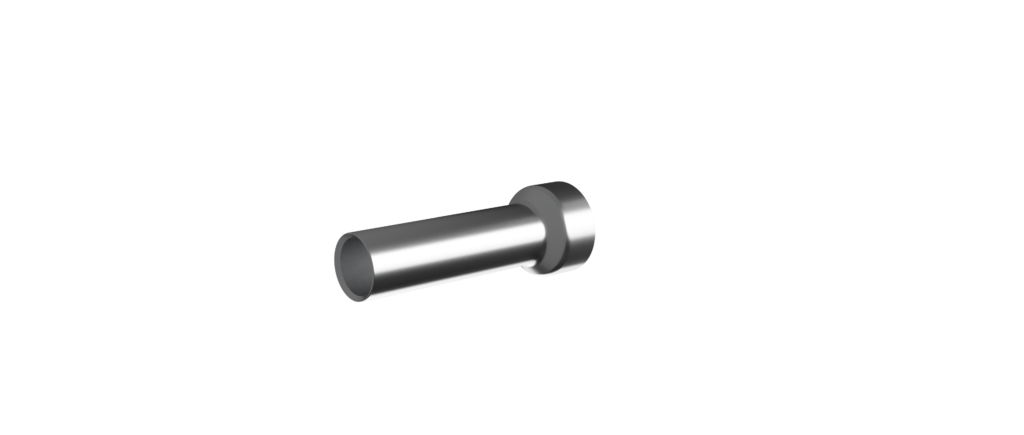
The tube-type load cell proved to be the best fit for our application. Since forces act naturally along the tube’s axis, the strain distribution is highly predictable, which enhances measurement accuracy. This design offers high stiffness while minimizing off-axis flexing, making it ideal for real-time force sensing.
After extensive analysis, we determined that the tube-type load cell offered the best balance of precision, robustness, and seamless integration into our adaptive system
Design and Engineering Process
Material Selection: 7075-T6 Aluminum
To ensure the load cell could handle both high and low force conditions while maintaining sensitivity, we selected 7075-T6 aluminum. This high-strength aluminum alloy provided the ideal balance of mechanical characteristics required for force sensing within the 20-400 lbs range.
Unlike stainless steel, which would have required excessively thin walls in our load cell to achieve the same range and sensitivity, aluminum allowed us to balance structural integrity and precision strain measurement. The thin walls with the stainless steel variant would’ve caused heat deformation during machining.
By choosing 7075-T6 aluminum, we ensured a manufacturable, high-performance, long-lasting load cell design that met our application’s specific needs.
Strain Gauge Selection
We selected the HT Sensor Technology Co. BF1000-3EB(23)-T0-F-X1-E strain gauge. This strain gauge features a gauge factor of 2.15 and a resistance of 1000 ohms, making it highly sensitive to strain variations. Additionally, it is a full-bridge strain gauge, meaning that only one gauge was required for force measurement, simplifying integration and reducing complexity.
Electronics & Signal Processing
Signal Amplification
Strain gauge signals are extremely small, making signal amplification a critical part of load cell design. For our design, at the lowest applied force of 20 lbs, the change in resistance was only 0.1Ω, necessitating a specialized instrumentation amplifier circuit to boost the signal while maintaining clarity.
Temperature Compensation
To ensure accurate force measurement, our circuit incorporated temperature compensation mechanisms, which prevented signal drift due to environmental fluctuations. Whether it’s a cold gym in winter or a warm workout studio in summer, 100 lbs should be 100 lbs, no matter what!
Development
Manufacturing
The load cell body was manufactured using CNC lathe machining with tolerances maintained within ±0.010”. These tight tolerances ensured force responses were predictably close to our design.
Assembly
After machining, the strain gauges were carefully bonded to the load cell using precision alignment tools and industrially approved processes. Proper alignment and bonding were crucial to ensure stable readings and efficient force conduction through the gauge.
Results
With the development of our custom tube-type load cell, we have created a system that enables real-time force sensing within an adaptive workout environment. When coupled with a torque motor, the load cell creates a closed-loop feedback system that dynamically adjusts resistance throughout a workout, keeping users in their optimal training zone. This allows for fatigue-aware training, automatically adapting to force fluctuations and preventing overexertion or inefficient workouts.
We see it as a New Fundamental—a core building block for the next generation of expressive, interactive machines that can truly feel the forces around them. This same technology could even be applied to musical instruments, such as our Magnetochord concept.