The Motivation
As music evolves towards becoming increasingly expressive, the technology that supports it must evolve too. As lovers of music and innovators, seeing the rise of MIDI MPE, new control surfaces, and performance techniques, we recognized a huge gap: physical instruments were not keeping up with digital expressiveness. While digital instruments are flexible, they often lack the visceral, emotional impact of a physical instrument.
From first principles, we envisioned an instrument that would seamlessly blend the natural expressiveness of stringed instruments with the dynamics and precision of modern electronic music. The result was the Magnetochord —a hybrid of pianos, synthesizers, and guitars—requiring an entirely new class of actuation: a motor capable of real-time, high-bandwidth control over string tension.
In other words, each string needs to be able to instantly re-tune and change tunings to support new paradigms like dynamic tonality, pitch modulation like guitar bends, and expressive vibrato.
Initial Explorations
We set out to discover the kinds of mechanisms that could help us achieve real-time string tension modulation. We explored, developed, and built prototypes for several different designs, each with its own set of challenges.
The issue with real strings is that they can break! Early simulations we developed revealed that an ideal mechanism should use linear motion to optimize stress distribution and ensure forces remain within fatigue limit tolerances. With this in mind, we tested a range of potential actuation methods.
Ball-Screw Based Actuation
Ball screws, widely used in precision machinery for their smooth, low-friction linear motion, were an early candidate. We built several prototypes using stepper and BLDC motors, but ran into several issues.
While they were capable of generating high torques and at holding tension precisely with minimal holding force, they suffered a number of issues.
- Mechanical Lag – The mechanical advantage provided by ball-screws also introduced excessive lag, which proved too slow for practical musical usage.
- Complex, Costly Control – The motors required more expensive controllers that wouldn’t scale across multiple strings.
- Sensitivity to Dust and Debris – Ball-screws are highly sensitive to contamination like dust, making them unsuitable for a rugged, real-world musical environment.
- Low Modulation Capability – The back and forth motion of vibrato creates a resonance in the ball-screw mechanism which causes the tuning drift over time.
Voice-Coil Based Actuation
Next, we turned to voice coil motors (VCMs), which offered excellent control and fast response times. However, they came with their own set of problems:
- Costly Magnets – High-performance VCMs require highly-custom, expensive magnet geometries.
- Limited Stroke Length – Standard voice coil motors lacked sufficient movement range for meaningful string tension modulation.
- Low Force – Traditional designs aren’t capable of generating the forces needed to sustain the required tensions.
Discovering the Design Principles
Through these failures, we were able to identify what our ideal solution needed to have:
- Direct Drive – Immediate responsiveness to player input
- High Force – capable of easily achieving the required string tensions
- Simple Control – Ability to control with simple algorithms
- Design for Manufacturing – Design parts for a minimal number of manufacturing operations.
- Real-World Ruggedness – Artists need an instrument that will hold up night after night
- Dynamic force control – Real-time force modulation for expressive playability.
With these guiding principles in mind, we set out to build something entirely new.
Custom Linear Motor
With conventional solutions falling short, we engineered a custom linear motor from the ground up. This meant extensive simulations, iterations, and deep-dives into electromagnetic design.
Research & Simulations
“An hour in the library can save a month in the laboratory”.
Before building physical prototypes, we conducted extensive electromagnet simulations by developing our own analytical tools and using FEMM software. These allowed us to optimize the magnetic flux path for improved force efficiency, ensuring a high-performance design before going to manufacturing.
Prototype Development
Each iteration brought us closer to the ideal solution.
Prototype 1: Basic Moving Magnet Design
This design featured a large magnet mounted on a piston, attracted towards a pole with a coil wrapped around it—essentially an enclosed electromagnet. While mechanically simple and easy to manufacture, it was inherently unstable. The control problem was akin to balancing a pencil on its point.
Prototype 2: Radial Flux Multi-Coil Design
Next, we were looking for a design that had linear control characteristics, high force output, and large stroke length. We landed on a design that used radially magnetized magnets and multiple commutated coils to achieve linear control and larger stroke length, but this had its own set of drawbacks:
- Cogging Effects – The piston experienced choppy motion due to the commutation
- Part Sourcing – Radially polarized magnets are much more costly to source
- Manufacturing Complexity – The coil arrangement makes manufacturing much more difficult
Breakthrough Prototype 3: Single Coil, Single Magnet Design
After much experimentation, our breakthrough design combined the strengths of earlier prototypes while overcoming their weaknesses.
- High Force, High Range – A unique magnetic circuit geometry stretched high-force over a larger usable range.
- Direct Drive – The single coil design provides smooth force delivery across the operating range without commutation.
- Simple Control – The motor is easily controllable
- Axially Polarized Magnets – Common and easily sourced, reducing cost.
- Simple Manufacturing – The overall motor construction is readily manufacturable using traditional CNC lathe operations.
Design for Manufacturing (DFM)
A key consideration from the beginning was manufacturability. Our final design leverages axially-polarized magnets, which are widely available, reducing cost and supply-chain constraints. Additionally the motor structure was optimized for production using CNC lathe operations. Finally, the system as a whole was designed to ensure simplified assembly by reducing dependencies and component count. By designing with DFM principles in mind, we ensured that our solution could scale from prototype to full production without major redesigns.
Results
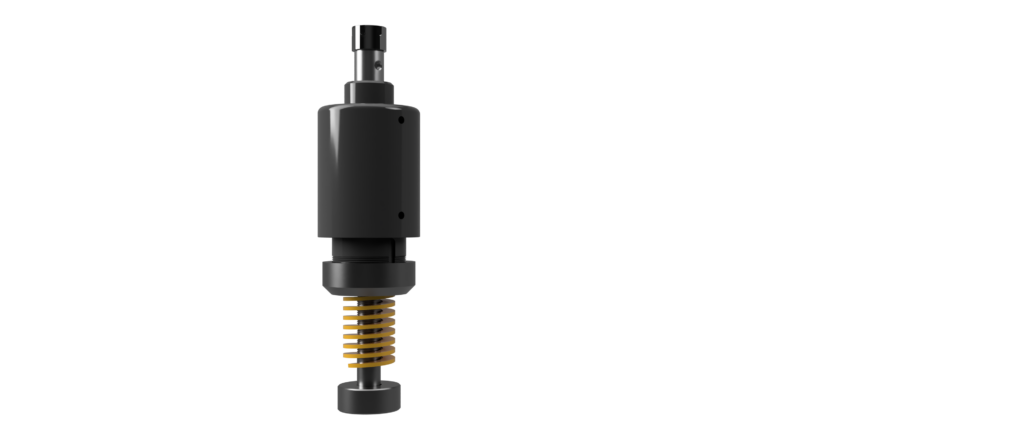
After extensive development, we finally arrived at a design delivering real-time string modulation, enabling expressive control.
While the current implementation was designed for the Magnetochord, we see the LM-001 as a New Fundamental for applications where the demanding combination of high-force, and expressive control is essential. Its potential extends far beyond music, becoming a core component for a newer class of expressive physical-digital hybrid machines.
We are excited to continue refining this technology, pushing the boundaries across multiple domains.